资讯
联系我们
公司名称:化工填料厂家
公司QQ:27749890
联系人:龙经理
业务电话:18779917026
联系地址:江西萍乡湘东陶瓷工业园
翅化技术提高共轭环填料传质性能的试验研究
2019-08-24 阅读:次
共轭环是我国自行开发的高效新型散堆填料,在气液传质过程中具有通量大、阻力小、传质效率高等特点,已在石油、轻工、等行业的精馏、吸收过程中得到广泛的应用,并应用于工艺的液液传质过程中¨ 。在过去提高填料传质效率的研究工作主要集中在填料宏观结构形状的设计和加工方面,国内外学者在建立光壁面填料塔内流态模型及其应用方面作了大量工作 “ ,使填料传质效率有所提高 。 目前大多数填料已比较接近理想填料,今后通过改进宏观几何尺寸来进一步提高传质效率是有限的。填料的表面特征的改善将是能否促进填料塔内气液相充分混合、提高传质效率的关键。对基料表面特征作进一步翅化改进,填料比表面积和空隙率,提高润湿性,减小压降,提高操作气流速度,在填料表层主动诱导、互扰形成均匀湍流层,加强气液传质相接触混合机会,为提高传质效率创造条件。
1 不锈钢薄板翅结构的生成
1.1 不锈钢板材表面的翅化加工
在不锈钢板表层实现翅化加工 (所谓表面翅化加工,是指在填料的基料表层通过机械加工的方法生成类似于百叶窗状的非贯穿性翼形结构)不同于通常在塑性金属表面进行的以挤压、塑性流动变形和劈斩、翻犁为主要特征的犁削翅化加工,在薄板材表层实现三维翅结构的成形以及通过刀具几何参数和加工工艺参数控制三维翅结构形状方面具有其性。笔者对在 0.1mm厚度的不锈钢带材表面翅结构形成机理及成形技术进行了试验探索。
在表层进行翅化加工时,关键是要能实现在薄板厚度内的微量切削,要求切削运动方向与材料表面基本平行,沿垂直于料厚方向的切削分力要尽可能小,理论上趋于零。翅化加工的方式是类似于采用圆柱形铣刀顺铣的断续切削,加工过程分为:①刀一 工接触滑擦、②刀具在材料表面耕犁和③翅结构形成三个阶段。在刀一工接触滑擦的一阶段里,刀具向材料表层切人,由于加工系统的变形,其中包括板料装夹装置的变形,机床系统的变形,刀具装夹装置的变形,刀具切削刃钝圆部分对被加工板料挤压使得被加工板料在刀具的作用下发生延展、弹塑性变形等因素,造成刀具切削刃不能切入被加工板料表层,只是在表面上滑擦、搓挤,被加工板料表层发生变形并伴有微量隆起;在刀具切人量进一步加深的情况下,二阶段产生了,切削刃继续向前方推挤材料,并将材料沿垂直于切削方向向两侧翻犁;当切削刃前方推挤的材料累积程度达到临界值时,加工过程进入三阶段,即翅结构形成 (或称切削起翅 )阶段,切削刃切人材料中,一变形区 (切屑形成变形区)内的材料经过了弹性变形和塑性变形,在剪切应力作用下,晶粒伸长呈纤维状;在二变形区(前刀面上内摩擦区)靠近前刀面的切屑底层的流动速度非常低,流向几乎与前刀面平行,部分粘附在前刀面上,切屑底层内发生剪切应变,出现滞流现象,切屑纤维中发生了显著的弯曲,发生二次塑性变形;在前刀面上产生了微小的积屑瘤,有少量微小金属碎块脱落;在三变形区(刃前变形区)刃前应力状态很复杂,应力区很小,应力数值却很大,经过刀刃的作用,使金属产生塑性变形和滑移分离,在切削刃分流点以上的被切削层材料经剪切区变成切屑流出(进而形成翅结构),分流点以下的很小一部分材料经受刀刃钝圆部分强烈挤压并由此产生很大的附加塑性变形后,留在已加工表面上,随后由于里层材料的弹性恢复和后刀面与已加工表面摩擦,使已加工表面再次发生塑性变形。从前刀面上流出的短小切屑,并未与材料表面分离,而是在进给运动的配合下留存在材料表面形成了翘起的翅结构,随后,翘起的翅结构进一步向材料表层翻起,翅的底层脱离前刀面,形成稳定的翅结构。翅结构的外表面与基料表面呈夹角 75。一85。翻起 (刀具 前角 -y。=20。、后角 。=20。、刃倾角 .=0。),翻起高度为 0.2—0.3mm,翅间距为 3—4 mm,翅结构的几何参数随刀具几何参数、切削用量和材料表面特性而变化。
当刃倾角 ks≠0。时 ,翅化加工过程就是斜角切削过程。采用斜角切削加工使流屑平面内的有效前角增加,刀刃变得更加锋利,使材料在剪切区的变形、切削力、摩擦系数等均较相应条件下的直角切削时有所减小,斜角切削在切屑流出方向上不有垂直于切削刃方向上的金属塑性流动分量,而且附加有平行于切削刃方向上的金属塑性流动分量,两者的合成运动形成了类似于锯切的现象,使切削过程平稳而轻快,有利于改善加工状况。试验证实,与直角切削相比较,当垂直于进给方向的切削刃宽度不变,刃倾角 ks=30。时,切削过程更平稳,一、二阶段的刀一工接触过程更长,加工出的翅的上表面上锯齿形缺口减少,减少了由此引起的应力集中现象,切屑表面更为平滑,保证了翅结构有较高的强度。在相同前角条件下,翅结构的外表面相对于基料表面呈夹角 70。一75。,翻起高度为 0.2—0.3mm,翅间距减小为 2—3mil,单个翅的表面积更大,翅之间排列更为密集和均匀。
1.2 不锈钢基料翅化加工中的刀具磨损
基料翅化加工采用了高速钢刀具,刀具前角 -y。 = 20。,后角 。=20。,刃倾角有两种规格 .=0。和hs=30。。加工中随着刀具运动轨迹的变化工作前角稍有,工作后角稍有减小。前后角的加大,使刀尖楔角减小,削弱了高速钢刀具切削刃口部位的强度。在切削不锈钢这样的塑性、韧性都较高的难加工材料时,当切削厚度小时,作用在刀具刃口上的力成比例,刀具刃口上切削力的,加剧了刀具的磨损,使刀具切削刃口很快被磨损,呈锯齿状,伴随着刀具的磨损和刀尖圆弧半径的,工件表面明显恶化,形成恶性,磨损了的刀具形态复制在了翅结构和滑擦过的表面上,使得这些表面更为粗糙,布满了纵向沟纹和横向鳞刺(或皱褶 )。试验观察显示,正是这些表面特征改善了填料的流体力学性能。在试验中,刀具的主要失效形式是由材料硬化所引起的沟纹磨损。
2 翅结构表面对提高传质性能的影响
2.1 翅结构对传质性能的影响
翅结构表面对传质性能的影响是基于填料表面的茸态(宏观与微观的表面粗糙化),先在基料表面生成三维翅结构,然后再压制成一定结构形状的共轭环。从对传质液体的水力学性能影响来看,粗糙化的表面扩大填料的比表面积,提高传质液体在填料表面的附着力,并使传质液体在填料表面充分润湿,形成薄的能均匀分布的液膜,减少填料表面所持液体量,空隙率,减少压降的上升,进而提高操作气流速度,加强气液的接触混合,为传质效率的提高创造了条件。当传质气体流过翅表面时,翻起的翅结构了气体流动,迫使气流急剧改变流动速度的方向和大小,对传质气体流动实现了主动诱导,促进气液混合和接触,使翅结构表面上的液膜表面中的液体单元发生湍动,改善局部小规模不良液体分布,大大加速了总的扩散速率,促进了传质过程的进行,提高了传质效率。
2.2 翅结构对提高共轭环填料性能的比较
填料的流体力学性能和传质性能是评价填料使用性能的两个宏观指标,本文采用常温常压下,在300mil解吸塔内以空气解吸富氧水,通过测定上、下端溶解氧浓度和压力差的方法来计算填料的传质和流体力学性能。测试样品采用 16mm不锈钢共轭环 (光 滑表面,未翅化 )与翅化的 16 mm 金属共轭环在相同外界条件下进行试验对比测试。
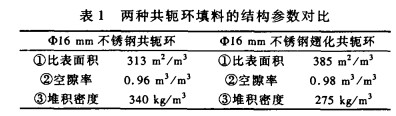
(1)填料表面的三维翅结构可提高液体在填料表面的润湿性。翅化加工后的共轭环的液体力学和传质性能明显于未加工的共轭环。翅化加工后的共轭环的传质单元高度 (H。),比未翅化的降低10%一20%,翅化加工后的共轭环的液膜传质系数kI.比未翅化的提高 10%一15%。
1 不锈钢薄板翅结构的生成
1.1 不锈钢板材表面的翅化加工
在不锈钢板表层实现翅化加工 (所谓表面翅化加工,是指在填料的基料表层通过机械加工的方法生成类似于百叶窗状的非贯穿性翼形结构)不同于通常在塑性金属表面进行的以挤压、塑性流动变形和劈斩、翻犁为主要特征的犁削翅化加工,在薄板材表层实现三维翅结构的成形以及通过刀具几何参数和加工工艺参数控制三维翅结构形状方面具有其性。笔者对在 0.1mm厚度的不锈钢带材表面翅结构形成机理及成形技术进行了试验探索。
在表层进行翅化加工时,关键是要能实现在薄板厚度内的微量切削,要求切削运动方向与材料表面基本平行,沿垂直于料厚方向的切削分力要尽可能小,理论上趋于零。翅化加工的方式是类似于采用圆柱形铣刀顺铣的断续切削,加工过程分为:①刀一 工接触滑擦、②刀具在材料表面耕犁和③翅结构形成三个阶段。在刀一工接触滑擦的一阶段里,刀具向材料表层切人,由于加工系统的变形,其中包括板料装夹装置的变形,机床系统的变形,刀具装夹装置的变形,刀具切削刃钝圆部分对被加工板料挤压使得被加工板料在刀具的作用下发生延展、弹塑性变形等因素,造成刀具切削刃不能切入被加工板料表层,只是在表面上滑擦、搓挤,被加工板料表层发生变形并伴有微量隆起;在刀具切人量进一步加深的情况下,二阶段产生了,切削刃继续向前方推挤材料,并将材料沿垂直于切削方向向两侧翻犁;当切削刃前方推挤的材料累积程度达到临界值时,加工过程进入三阶段,即翅结构形成 (或称切削起翅 )阶段,切削刃切人材料中,一变形区 (切屑形成变形区)内的材料经过了弹性变形和塑性变形,在剪切应力作用下,晶粒伸长呈纤维状;在二变形区(前刀面上内摩擦区)靠近前刀面的切屑底层的流动速度非常低,流向几乎与前刀面平行,部分粘附在前刀面上,切屑底层内发生剪切应变,出现滞流现象,切屑纤维中发生了显著的弯曲,发生二次塑性变形;在前刀面上产生了微小的积屑瘤,有少量微小金属碎块脱落;在三变形区(刃前变形区)刃前应力状态很复杂,应力区很小,应力数值却很大,经过刀刃的作用,使金属产生塑性变形和滑移分离,在切削刃分流点以上的被切削层材料经剪切区变成切屑流出(进而形成翅结构),分流点以下的很小一部分材料经受刀刃钝圆部分强烈挤压并由此产生很大的附加塑性变形后,留在已加工表面上,随后由于里层材料的弹性恢复和后刀面与已加工表面摩擦,使已加工表面再次发生塑性变形。从前刀面上流出的短小切屑,并未与材料表面分离,而是在进给运动的配合下留存在材料表面形成了翘起的翅结构,随后,翘起的翅结构进一步向材料表层翻起,翅的底层脱离前刀面,形成稳定的翅结构。翅结构的外表面与基料表面呈夹角 75。一85。翻起 (刀具 前角 -y。=20。、后角 。=20。、刃倾角 .=0。),翻起高度为 0.2—0.3mm,翅间距为 3—4 mm,翅结构的几何参数随刀具几何参数、切削用量和材料表面特性而变化。
当刃倾角 ks≠0。时 ,翅化加工过程就是斜角切削过程。采用斜角切削加工使流屑平面内的有效前角增加,刀刃变得更加锋利,使材料在剪切区的变形、切削力、摩擦系数等均较相应条件下的直角切削时有所减小,斜角切削在切屑流出方向上不有垂直于切削刃方向上的金属塑性流动分量,而且附加有平行于切削刃方向上的金属塑性流动分量,两者的合成运动形成了类似于锯切的现象,使切削过程平稳而轻快,有利于改善加工状况。试验证实,与直角切削相比较,当垂直于进给方向的切削刃宽度不变,刃倾角 ks=30。时,切削过程更平稳,一、二阶段的刀一工接触过程更长,加工出的翅的上表面上锯齿形缺口减少,减少了由此引起的应力集中现象,切屑表面更为平滑,保证了翅结构有较高的强度。在相同前角条件下,翅结构的外表面相对于基料表面呈夹角 70。一75。,翻起高度为 0.2—0.3mm,翅间距减小为 2—3mil,单个翅的表面积更大,翅之间排列更为密集和均匀。
1.2 不锈钢基料翅化加工中的刀具磨损
基料翅化加工采用了高速钢刀具,刀具前角 -y。 = 20。,后角 。=20。,刃倾角有两种规格 .=0。和hs=30。。加工中随着刀具运动轨迹的变化工作前角稍有,工作后角稍有减小。前后角的加大,使刀尖楔角减小,削弱了高速钢刀具切削刃口部位的强度。在切削不锈钢这样的塑性、韧性都较高的难加工材料时,当切削厚度小时,作用在刀具刃口上的力成比例,刀具刃口上切削力的,加剧了刀具的磨损,使刀具切削刃口很快被磨损,呈锯齿状,伴随着刀具的磨损和刀尖圆弧半径的,工件表面明显恶化,形成恶性,磨损了的刀具形态复制在了翅结构和滑擦过的表面上,使得这些表面更为粗糙,布满了纵向沟纹和横向鳞刺(或皱褶 )。试验观察显示,正是这些表面特征改善了填料的流体力学性能。在试验中,刀具的主要失效形式是由材料硬化所引起的沟纹磨损。
2 翅结构表面对提高传质性能的影响
2.1 翅结构对传质性能的影响
翅结构表面对传质性能的影响是基于填料表面的茸态(宏观与微观的表面粗糙化),先在基料表面生成三维翅结构,然后再压制成一定结构形状的共轭环。从对传质液体的水力学性能影响来看,粗糙化的表面扩大填料的比表面积,提高传质液体在填料表面的附着力,并使传质液体在填料表面充分润湿,形成薄的能均匀分布的液膜,减少填料表面所持液体量,空隙率,减少压降的上升,进而提高操作气流速度,加强气液的接触混合,为传质效率的提高创造了条件。当传质气体流过翅表面时,翻起的翅结构了气体流动,迫使气流急剧改变流动速度的方向和大小,对传质气体流动实现了主动诱导,促进气液混合和接触,使翅结构表面上的液膜表面中的液体单元发生湍动,改善局部小规模不良液体分布,大大加速了总的扩散速率,促进了传质过程的进行,提高了传质效率。
2.2 翅结构对提高共轭环填料性能的比较
填料的流体力学性能和传质性能是评价填料使用性能的两个宏观指标,本文采用常温常压下,在300mil解吸塔内以空气解吸富氧水,通过测定上、下端溶解氧浓度和压力差的方法来计算填料的传质和流体力学性能。测试样品采用 16mm不锈钢共轭环 (光 滑表面,未翅化 )与翅化的 16 mm 金属共轭环在相同外界条件下进行试验对比测试。
试验结果表明,两种共轭环填料在具有相同填料层高度情况下,翅化加工后的共轭环的流体压降减小 10% 一30%,两者压降与空塔气速之间关系曲线(AP/Z—U(m/s))相近,但求得的泛点气速却有一定的差异,在相同的喷淋密度 L(m •m一 •h )情况下,后者的泛点气速 U (m/s)明显大于前者,并且随着喷淋密度的,后者泛点气速增长大于前者。由此可见,翅化加工后的共轭环表面与水的接触角 0小于光滑的共轭环表面与水的接触角,进而提高了填料的表面润湿性,允许泛点气速进一步提高,加大了持液量由静态转为动态的机会,使湍动,为加强传质相的接触混合,提高传质效率创造了条件。
对实验结果进行整理,传质单元高度和传质系数表示如下:
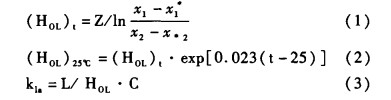
结果表明,翅化加工后的共轭环的传质性能明显于未加工过的共轭环,翅化加工后的共轭环的传质单元高度 (H。):,比未翅化的降低 10% 一20%,翅化加工后的共轭环的液膜传质系数 k。.比未翅化(光滑表面)的提高 10% 一15%。很显然,翅化共轭环液体力学和传质性能的改善是得益于其表面粗糙化的特征变化。
结论
对利用填料表面三维茸状翅结构提高填料性能进行的试验结果分析认为:结果表明,翅化加工后的共轭环的传质性能明显于未加工过的共轭环,翅化加工后的共轭环的传质单元高度 (H。):,比未翅化的降低 10% 一20%,翅化加工后的共轭环的液膜传质系数 k。.比未翅化(光滑表面)的提高 10% 一15%。很显然,翅化共轭环液体力学和传质性能的改善是得益于其表面粗糙化的特征变化。
结论
(1)填料表面的三维翅结构可提高液体在填料表面的润湿性。翅化加工后的共轭环的液体力学和传质性能明显于未加工的共轭环。翅化加工后的共轭环的传质单元高度 (H。),比未翅化的降低10%一20%,翅化加工后的共轭环的液膜传质系数kI.比未翅化的提高 10%一15%。
(2)提高空隙率、减小压降,翅化加工后的共轭环的流体压降可减小 10% 一30%,操作气流速度可进一步提高,使填料塔操作良好,传质效率得以提高。在压力降相同的条件下,具有茸状形貌特征表面的填料传质效率与光滑表面结构填料传质效率相比,可提高 l0% 一12%。
(3)虽然翅化加工增加了填料的生产成本,但可以通过空隙率的,减少填料使用个数来抵偿总成本的提高,关键是随着传质性能的提高使得使用者的投入与产出效益比提高。
可见,利用填料表面三维茸状翅结构提高填料传质性能是切实可行的。有关填料对试验结果给予高度评价,认为是进一步提高填料性能的理想方法。
